What is the effect of GRC components used for exterior wall decoration? Hainan Sculpture I will introduce you.
The high performance modification of cement has always been an important part of GRC material technology. The solution of these technical problems has made GRC enter an important milestone on the zigzag road of development, and has also made fundamental changes to the problems that have plagued the development of GRC for a long time. The double insurance technology route previously adopted in China, that is, using low alkali sulphoaluminate cement and alkali resistant glass fiber composite method to produce GRC products, has solved the corrosion problem of alkali resistant glass fiber in high alkaline environment, but the strength of low alkali sulphoaluminate cement will be reduced in the later period, the hardening speed is too fast, and the manufacturers of such cement are mixed, The application of GRC plate in curtain wall is restricted by the influence of low output and various reasons. In order to overcome these problems with GRC materials, Portland cement should be used again.
① Adding fine mineral admixtures with high pozzolanic activity to Portland cement
Adding fine mineral admixtures with high pozzolanic activity in Portland series cement, its main function is to make SiO2 in fine mineral admixtures with pozzolanic activity react with Ca (OH) 2 generated by cement hydration to generate CSH, thus reducing the alkalinity of cement matrix pore solution and reducing the generation of Ca (OH) 2 crystals. Some fine admixtures also contain a certain amount of Al2O3;, It can also react with Ca (OH) 2 under certain conditions. The pozzolanic active fine admixtures tested so far include fly ash, silica fume and metakaolin.
② Adding some polymer emulsion to Portland cement
Adding polymer emulsion to Portland series cement base materials can play the following roles: ① polymer fine particles (particle size~0.1 μ m) Preferentially entering the channel of alkali resistant glass fiber precursor can prevent Ca (OH) 2 crystal from crystallizing and growing in the channel without damaging the fiber; ② The polymer can form a film to protect the fiber, thus reducing the chemical attack of high alkalinity pore solution on the fiber. However, according to the research results of the Netherlands and the United Kingdom [16] [17], whether the addition of polymer emulsion can improve the long-term durability of GRC in wet environments depends largely on the water resistance of the formed polymer film. The British Building Research Institute (BRE) once mixed polyacrylate emulsion, styrene butadiene latex, propylbenzene emulsion, etc. into Portland cement substrate to match with alkali resistant glass fiber to produce GRC. Although the attenuation rate of mechanical properties of GRC mixed with the above emulsion in the atmosphere is significantly lower than that of GRC without emulsion, immersion in normal temperature water does not show its superiority. Jacobs and Bijen in the Netherlands use modified polyacrylate emulsion "Forton" to add to Portland cement, which can be made with alkali resistant glass fiber into GRC with good durability and immersion in water.
GRC mixed with polymer emulsion is often referred to as PGFRC (abbreviation for Ploymer Modified Glass Fiber Reinforced Cement, which means polymer modified GRC), and has been widely used in the United States to make building cladding. According to the summary and analysis of a series of test results, it is believed that the amount of polymer has a great impact on the improvement effect of GRC durability. In order to achieve a better effect, the amount of polyacrylate solids in Forton emulsion should not be less than 7% of the weight of cement Up to now, the flexural mechanical properties of PGFRC doped with Forton emulsion have been measured after 14 years of exposure in the atmosphere. The results show that the MOR value of the latter is significantly higher than that of the former (about 43% higher) after 1 year, 2 years, 5 years, 11 years and 14 years of comparison of the flexural properties of two GRCs doped with 7.7% polymer emulsion in the atmosphere, The major difference between the two is that the latter still maintains high ductility (the retention rate of tensile failure strain is more than 60%), while the former is completely brittle (the retention rate of tensile failure strain is only 2%). It can be seen that adding appropriate amount of polymer emulsion into GRC is obviously beneficial to the long-term durability of the composite. More about Hainan sculpture Hainan GRC component 、 Hainan EPS component Please pay attention to the official website of Hainan Jin'ao Garden Sculpture Art Co., Ltd.
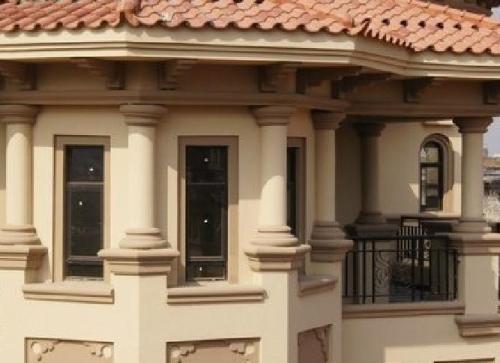