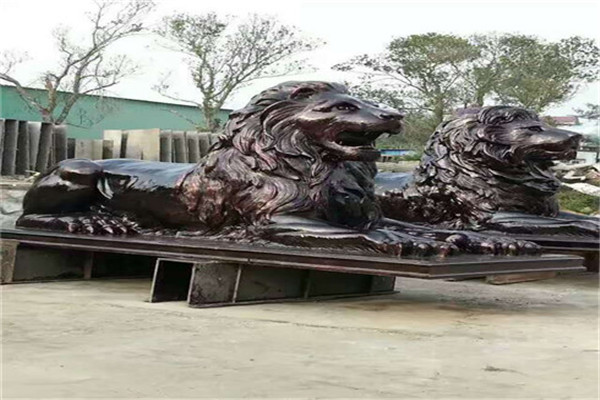
The traditional method is to brush lime water or wall powder, but it is easy to be polluted and cannot be scrubbed with wet method. It is mostly used for general buildings. More advanced buildings use flat ready mixed paint as decoration material, which is rich in color and is not easy to be polluted, but the volatile amount of organic solvent mixed in is large, which pollutes the atmosphere and affects the health of construction personnel. With the development of science, organic synthetic resin raw materials are widely used in paint, making the appearance of paint products fundamentally changed, so it is called paint, It has become an important interior and exterior wall decoration material. There is a long history of papering interior walls and ceilings, but it has been replaced by plastic wallpaper and fiberglass wall covering. Hainan sculpture gypsum board has the characteristics of fire prevention, sound insulation, heat insulation, light weight and high strength, and convenient construction, which is mainly used for walls and flat roofs; When making a flat roof, holes with various patterns can be punched to improve the sound absorption and decoration effect. Calcium plastic board has a good decorative effect, can keep warm and sound, and is a multi-functional board. Marble and granite plates are increasingly used to decorate high-end hotels and apartments.
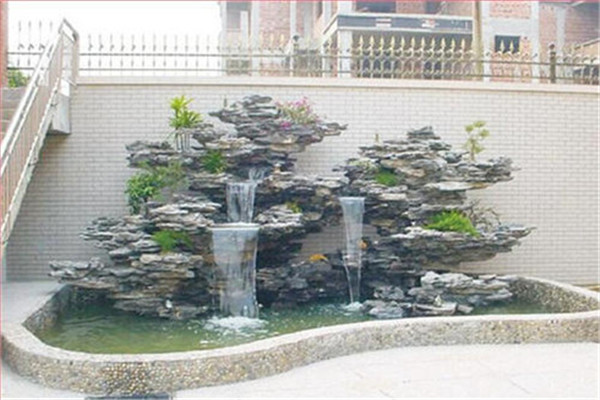
Wood carving is a kind of sculpture, which is often called "folk craft" in our country. Headwater of river EPS line Wood carving can be divided into three categories: three-dimensional round carving, root carving and relief carving. Wood carving is a kind of work separated from carpentry, which is classified as "fine carpentry" in our country. Folk art varieties classified by carving materials. Generally, the tree species with fine and tough texture and not easy to deform are selected, such as nanmu, red sandalwood, camphor wood, cypress, ginkgo, agarwood, mahogany, longan, etc. The tree root carving art in natural form is called "tree root carving". Wood carving has round carving, relief carving, engraving or several techniques. Some are also painted to protect wood and beautify it. recommend EPS line Generally speaking, tools for wood carving creation, such as saws, wood files, chisels, carving knives, flat shovels, axes, wood drills, wood hammers, planes, etc., can be used for root carving creation. In addition, you also need basic tools such as scissors (scissors for pruning), knives, brushes, sandpaper (cloth), coarse and fine cloth, cotton yarn, rope, etc. During special processing, such as fire roasting, steaming, and insect prevention, some tools are also needed, which can be used in general families instead of other tools.
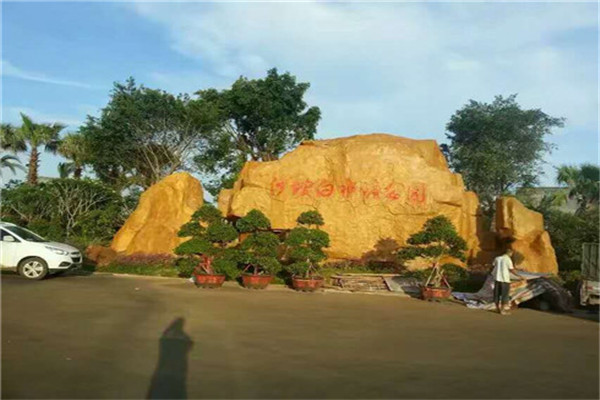
Marble, granite, Hui'an stone, Qingtian stone, Shoushan stone, Guicui stone and other materials are generally used for stone carving. Granite and marble are suitable for carving large statues; Qingtian stone and Shoushan stone are rich in color, which are more suitable for small stone carvings. There are many ways to make stone carvings. According to the nature of stone materials and the habits of the carvers, stone carvings can be roughly divided into two types: first, traditional methods. Conception, composition, modeling and stone carving are all done by individuals alone. For large-scale carving of lines, the horizontal and vertical lines shall be drawn on the stone, the grid shall be made to take materials, and the simple measurement and positioning method shall be used for carving. The second is to adopt a new process, that is, first make a clay sculpture, turn it into a plaster statue, then take the plaster statue (model) as the basis, rely on the point shaped instrument, and then carve it into a stone statue.
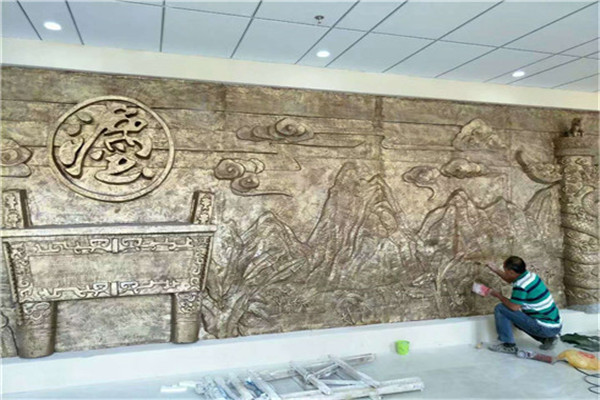
When people talk about jade cultivation, the word "cultivation" not only tells us that jade is a living substance, but also contains a lot of knowledge. The maintenance of jade jewelry can be summarized as follows: the hardness of jade is very high, but it is easy to crack after collision. Sometimes, although the cracks cannot be seen with the naked eye, the molecular structure in the surface of jade has been damaged, with dark cracks, which greatly damages its perfection and economic value. Avoid dust as much as possible. If there is dust on daily jadeware, it should be cleaned with a soft brush; If dirt or oil stains are attached to the surface of the jade, they should be brushed with mild soapy water, and then washed with clean water. Do not use chemical degreasing agent or degreasing fluid. It is better to put it in the jewelry bag or jewelry box to avoid scratches or damage. If it is high-grade jade jewelry, do not place it on the counter to avoid dust and affect the transparency. Try to avoid contact with perfume, chemicals, soap and human sweat. If jade is exposed to too much sweat and is not wiped clean immediately after wearing, it will be eroded, causing damage to the outer layer and affecting the original brightness. Especially the "glass ground" jadeite and white sheepskin jade, which also avoid sweat and grease. Jade should be protected from the sun, because the expansion of jade in case of heat will affect its quality. Hibiscus jade, crystal, agate, etc. may even burst under high heat. Wipe the accessories with clean and soft white cloth, not with dyed cloth or hard fiber cloth. Jade jewelry inlaid with diamonds, rubies, emeralds and other precious stones should only be wiped with a clean white cloth to remove grease, dust, etc., which helps maintain and maintain the original quality. Keep proper humidity. The quality of jade depends on a certain humidity, especially for aquabilite and crystal jade. The surrounding environment shall not be too dry.
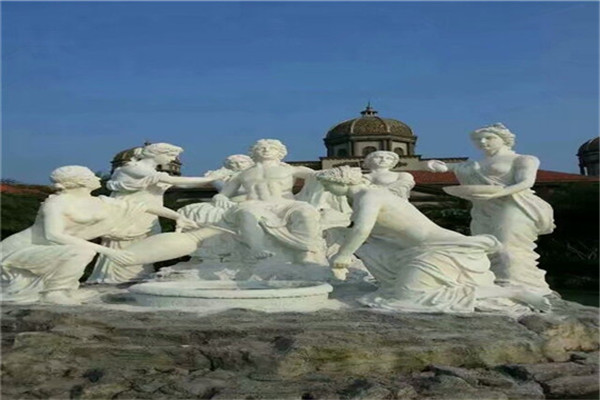
Copper casting is an important part of Chinese traditional culture and art. Copper casting has a long history and mature technology. The process of casting copper is more complicated than that of forging copper, and the artistic creation has a good recovery. Therefore, it is suitable for becoming the material of fine works and is very popular with artists, especially figure sculpture. But it is easy to oxidize, so pay more attention to maintenance. Each cast copper artwork is made through 11 complex and rigorous processes, which include traces of traditional handicrafts, lines and modern technology of precision casting. Cast copper is put into the sintering furnace and sintered at 1000 ℃ - 1150 ℃ according to different metal materials. The copper liquid is immediately cast into the ceramic shell. After cooling, the outer ceramic shell is broken, and the copper product rough embryo is peeled out.