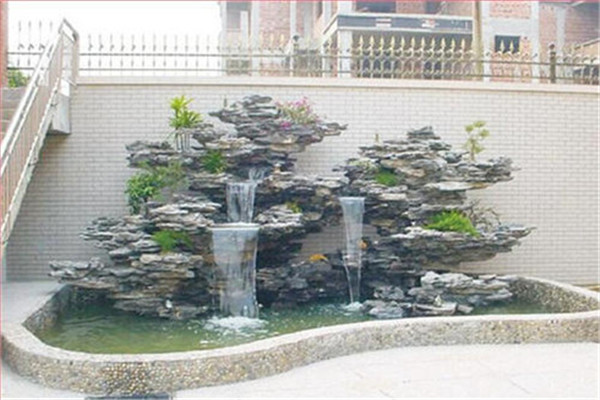
1. Traditional green sculpture shaping: directly pruning the plants with garden art. There are simple geometric shaping (such as sphere, cube, pyramid, cylinder), complex geometric shaping (layered shaping, spiral shaping, etc.), animal shaping and various peculiar shaping (automobile shaping, aircraft shaping, abstract and free shaping, etc.). Common plants include pine and cypress, privet, boxwood, national locust, elm, etc. 2. Grafting: taking a certain plant as the rootstock, grafting plants with different impressions on it, and then making artistic processing of its shapes, such as polychrome chrysanthemum bonsai, polychrome rose bonsai, polychrome peach, polychrome plum, polychrome crabapple, etc. Such as cliff chrysanthemum, tower chrysanthemum, animal shaped chrysanthemum, etc. 2.1 Single plant green sculpture refers to the sculpture formed entirely by one plant or one plant with multiple colors or by grafting multi-color plants. The sculpture has a long viewing period and simple operation. For example, tree sculptures can be kept for a long time only by special pruning, without considering flower changing and water spraying, and the maintenance management is simple. 2.2 Double plant green sculpture refers to the sculpture shaped by two different kinds of plants. The sculpture has a long viewing period and a strong three-dimensional sense. It is usually modeled with the complementary and mutually reinforcing advantages of two plants. Such as evergreen and deciduous plants, broad-leaved and coniferous plants, lianas and herbs, as well as different colors, species, branches and leaves, such as leaf color, flowers and fruits, branches and stems. 2.3 Mixed plant green sculpture refers to sculpture with three or more kinds of plants. The sculpture has a short viewing period and complicated operation, but it is highly ornamental and lifelike. The common ones are large three-dimensional sculptures, some animal shaped sculptures elaborately composed of flowers, leaves and fruits of different plants according to design requirements, such as peacock, red crowned crane, panda, etc; Or symbolic sculptures with certain cultural connotation and city image, such as idiom allusion sculptures (learning to walk in Handan, dancing at the smell of chickens), Olympic seal, football World Cup, etc.
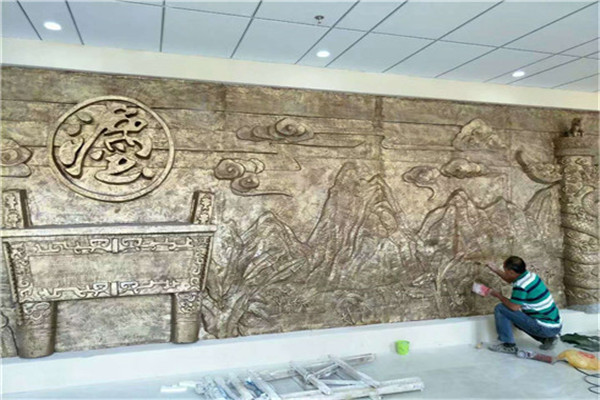
In the process of tourism development, Hefei Stone sculpture The landscape already exists. From the domestic Terracotta Warriors and Horses, the Shinto of the Ming Tombs, Dunhuang Grottoes, etc., a large number of tourists at home and abroad have been attracted. In recent years, Beijing Shijingshan International Sculpture Park, Miyun Legal Park, Changchun Sculpture Park, and OCT Sculpture Park, a number of urban theme parks, are also attracting tourists from all walks of life. Foreign theme sculpture parks such as Vigeland Sculpture Park, Seattle Olympic Sculpture Park, South Korean Sex Sculpture Park, etc. also attract many tourists. Here, the theme sculpture park and Stone sculpture Price Classify the similar tourist areas, find out the commonness and difference among them, and provide reference for the application of sculpture landscape in tourism development.
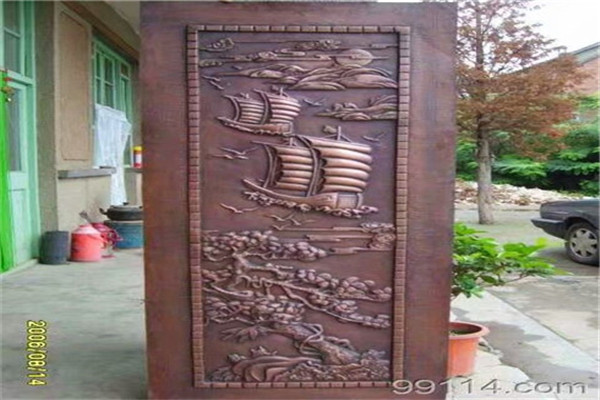
Exterior wall decorative panel is a new type of integrated material for building exterior wall decoration and insulation developed in recent years, which is composed of polyester baking paint or fluorocarbon paint, carved aluminum zinc alloy steel plate, polyurethane insulation layer and glass fiber cloth; It is mainly used for exterior wall decoration and energy-saving reconstruction of gymnasiums, libraries, school and hospital office buildings, villas and other buildings; The main functions are building decoration, heat preservation, energy conservation, heat insulation, sound insulation, waterproof and mildew proof. The metal surface decorative insulation board is a large external hanging wall board produced in industrialization. It has good durability and low maintenance cost due to dry installation construction. It integrates the external wall insulation and decoration functions, conforms to the development direction of building energy conservation "modularization" technology, and is an advanced technology vigorously promoted in the field of external temperature protection technology of building walls in China.
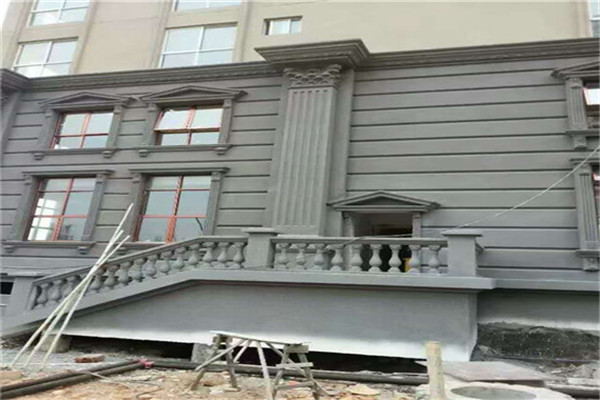
First of all, make the structural layer of the steel bar mountain mesh on the stone wall. According to the Hainan sculpture stone structure, the density of the steel bar is about 30 to 50 cm. Then, bind and weld the steel bar on the exposed steel bar head. Pay attention to the need to shape the approximate shape. After the steel bar is welded, tie a layer of steel wire mesh outside, and then start painting. The first painting is to make a base. For the second painting and shaping, it is necessary to make some rock texture, such as concave and convex, wrinkles, because the above steps must be grasped, and craftsmen must make the surface very artistic! Must have basic skills of modeling and stone molding. It is effective to spray stone like paint. Before large-area spraying, small samples were tested to show speckled particles in natural stone. Fill the gaps in the stone wall with earth and then plant them. Maybe fill some ceramic bottles and jars that are harmonious with the theme materials. There are still some water sources in the pottery to supplement its spatial diversity. There is also a new type of plastic stone, which is made of light materials such as environment-friendly building raw materials, fine resins, efficient reinforcing agents, pro aggregate, imported pigments, etc., by mixing, processing, and molding, and then steaming and curing at high temperature. Each product has different shapes and various combinations, which are no different from real stones in texture, color and texture.
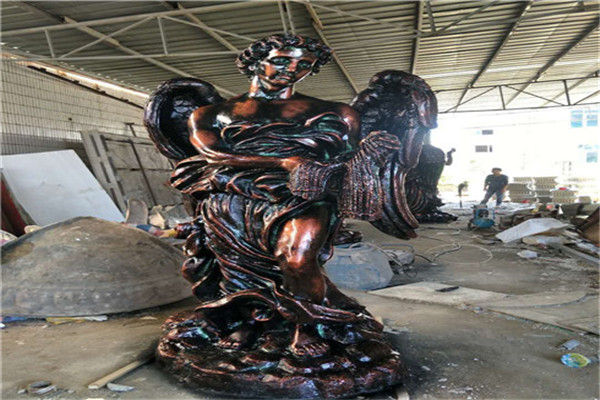
Copper casting is an important part of Chinese traditional culture and art. Copper casting has a long history and mature technology. The process of casting copper is more complicated than that of forging copper, and the artistic creation has a good recovery. Therefore, it is suitable for becoming the material of fine works and is very popular with artists, especially figure sculpture. But it is easy to oxidize, so pay more attention to maintenance. Each cast copper artwork is made through 11 complex and rigorous processes, which include traces of traditional handicrafts, lines and modern technology of precision casting. Cast copper is put into the sintering furnace and sintered at 1000 ℃ - 1150 ℃ according to different metal materials. The copper liquid is immediately cast into the ceramic shell. After cooling, the outer ceramic shell is broken, and the copper product rough embryo is peeled out.